4.3.1. Почему на грузовых вагонах применяется только рычажный, а на пассажирских рычажный и стержневой приводы автоматического регулятора тормозной рычажной передачи?
При торможении привод 2 (см. рис. 3) автоматического регулятора тормозной рычажной передачи приходит в контакт с корпусом 3. Возрастание тормозного усилия при увеличении давления в тормозных цилиндрах вызывает упругую деформацию тормозной рычажной передачи, и привод автоматического регулятора перемещает его корпус, сжимая возвратную пружину 4 с силой 170—200 кгс.
При стержневом приводе силу возвратной пружины регулятора вычитают из усилия, передаваемого тягами. На пассажирских вагонах это усилие в процентном отношении составляет небольшую долю от максимального тормозного усилия на тягах и практически не уменьшает расчетное тормозное нажатие. На грузовых же вагонах, особенно на порожнем режиме с композиционными тормозными колодками, это усилие может на 30 40% уменьшить расчетное нажатие тормозных колодок, так как передаваемая тягами сила соизмерима с силой сжатия возвратной пружины регулятора. При рычажном приводе значительно уменьшается отрицательное влияние авторегулятора на эффективность торможения, так как рычажный привод передает тягам только часть силы возвратной пружины регулятора.
При авторегуляторе № 574Б в отличие от авторегулятора № 536 привод на ступени торможения, как правило, не взаимодействует с корпусом (он вступает в контакт с корпусом при полном торможении либо, если тормозные колодки изношены от длительных торможений, на ступени без применения полного торможения), поэтому эффективность торможения на ступени при аворегуляторе № 574Б не уменьшается. Регулятор № 574Б по мере износа тормозных колодок обычно сокращает рычажную передачу при больших ступенях и полных торможениях, а также при отцепке локомотива от состава, когда разряжается тормозная магистраль. В автрегуляторе № 536 привод взаимодействует с корпусом при любой ступени торможения и влияет на эффект торможения при появлении на тягах усилия 300—500 кгс.
4.3.2. Какова особенность работы автоматического регулятора тормозной рычажной передачи на крутом затяжном спуске?
Регуляторы автоматически стягивают рычажную передачу при отпуске тормоза. При торможении происходит подготовка к регулированию, а сам регулятор работает, как обычная тяга, т. е. с износом колодок увеличивается выход штока. У регуляторов со стержневым приводом из-за интенсивного износа тормозных колодок может происходить сжатие возвратной пружины 4 (см. рис. 3) до соприкосновения витков. В этом случае тормозные усилия передаются на привод, что приводит к уменьшению тормозного эффекта, изгибу стержня привода и выходу из строя регулятора. Поэтому при следовании по затяжным спускам необходимо управлять автотормозами, периодически производя полный отпуск.
Нормальное действие авторегулятора обеспечивается, если полный отпуск тормозов (даже на непродолжительное время) делать 1 раз в среднем на каждые 4—6 км движения в тормозном режиме или чаще.
4.3.3. Почему на грузовых вагонах тормозные башмаки имеют жесткую посадку на триангель, а на пассажирских — шарнирное соединение с тормозной балкой?
Способ закрепления тормозного башмака определяется конструкцией тележки вагона и тем, расположены ли кроншейны подвесок на обрессоренной или необрессоренной части. На грузовых вагонах кронштейны крепления подвесок триангелей расположены на необрессоренных боковинах. В этом случае независимо от прогиба рессор под воздействием загрузки либо при вертикальных колебаниях положение тормозной колодки относительно колеса не изменяется, что позволяет жестко соединить башмак с триангелем. На пассажирских вагонах кронштейны подвесок располагаются на обрессоренных частях, вследствие чего при вертикальных колебаниях в процессе движения, а также при различной загрузке вагонов тормозная колодка перемещается относительно центра колеса, что требует шарнирного соединения башмака с тормозной балкой для равномерного распределения при торможении давления в контакте колодки и колеса.
4.3.4. Как выбирается передаточное число тормозной рычажной передачи?
При проектировании подвижного состава обязательной является унификация тормозных цилиндров и рычагов тормозной передачи. Так, для пассажирских и четырехосных грузовых вагонов с колодочным тормозом и одним тормозным цилиндром используются цилиндры с внутренним диаметром 356 мм (14″); для восьмиосных грузовых вагонов этого диаметра оказывается недостаточно, поэтому на них применяют тормозные цилиндры с внутренним диаметром 400 мм (16″).
Рычажные передачи тележек ЦНИИ-ХЗ-0 всех четырехосных грузовых вагонов одинаковы, также не отличаются рычажные передачи тележек КВЗ-ЦНИИ пассажирских вагонов (кроме габарита РИЦ), унифицированы рычажные передачи тележек восьмиосных полувагонов и цистерн. На пассажирских вагонах применяют три типа горизонтальных рычагов в зависимости от тары.
При выборе передаточного числа учитывают условия работы тормоза на крутом затяжном спуске, когда длительно не производится полный отпуск и поэтому авторегулятор не уменьшает выход штока. В таком режиме торможения общий расчетный объемный износ чугунных тормозных колодок, действующих на одно колесо, может достигать 250 см3 (это значение поддается расчету и подтверждается экспериментально). С учетом выхода штока тормозного цилиндра Нупр от упругих деформаций рычажной передачи и дополнительного хода поршня от износа тормозных колодок общий выход штока не должен превышать Нмах Из этого условия максимально допустимое передаточное число
Для расчета можно принять FK = 305 см2; Нмах=18 см; Нупр = 6 см для четырехосных грузовых и 7 см для пассажирских вагонов. По формуле находим: для грузовых вагонов nмах=9, для пассажирских nмах=12.
На тяговом подвижном составе обычно используются многоцилиндровые установки со значительно меньшим передаточным числом, которое обеспечивает условия работы рычажной передачи с меньшими углами наклона рычагов, а при отсутствии авторегулятора требуется меньшее число ее регулировок по мере износа колодок. Вместе с тем на локомотивах максимальное передаточное число рычажной передачи достигает 15 (тепловозы ТЭ10) и 16 (тепловозы (ТЭ7). Такое передаточное число допустимо в связи с большей площадью трения колодок (FK — 425 см2) и более жесткой рычажной передачей, имеющей меньшие упругие деформации, чем на вагонах.
Выбранное передаточное число рычажной передачи в сочетании с диаметром тормозного цилиндра и расчетным давлением в нем сжатого воздуха должно обеспечивать необходимые нормативы расчетного нажатия. Действительное суммарное (кгс) нажатие тормозных колодок, действующих от одного тормозного цилиндра, рассчитывают по формуле
Коэффициент потерь на трение принимают для тормозного цилиндра 0,98, а для рычажной передачи — в зависимости от ее кинематической схемы (0,95 — у четырехосных грузовых вагонов с односторонним нажатием колодок; 0,80 — у восьмиосных вагонов; 0,90 — у пассажирских вагонов; для локомотивов с двусторонним нажатием колодок 0,9 -• при действии цилиндра на одну ось, 0,85 — на две оси. 0,8 — на три оси; для локомотивов с односторонним нажатием 0,95 при действии тормозного цилиндра на две оси, 0,90— на три).
При достаточно жесткой рычажной передаче с небольшим числом последовательных звеньев целесообразно применение тормозных цилиндров большого диаметра с минимальным передаточным числом рычажной передачи.
Расчетное давление в тормозных цилиндрах принимают для локомотивов и пассажирских вагонов 3,8 кгс/см2, для грузовых вагонов: на порожнем режиме 1,6, среднем 2,8, груженом 4,0 кгс/см2.
4.3.5. С какой целью в композиционных тормозных колодках вместо стальной спинки используется сетчатопроволочный каркас?
Промышленность выпускает композиционные колодки усовершенствованной конструкции с сетчатопроволочным каркасом вместо стальной спинки. Применение такого каркаса обеспечивает повышение срока службы триозной колодки более чем на 10% в связи с допустимой при этом менышей предельной толщиной колодки 10 вместо 14 мм. Это оказалось возможным из-за отсутствия у новой колодки шипов для удержания на спинке фрикционной массы, которая лимитирует минимальную толщину композиционных колодок со стальной спинкой. Кроме того, сетчатопроволочный каркас обеспечивает более высокую вибрационную прочность.
В металлическом каркасе, особенно при повышенных скоростях движения и большом сроке службы колодок, возникают трещины в месте соединения ушка и спинки колодки. Колодки с сетчатопроволочным каркасом имеют практически неограниченную вибрационную стойкость и надежно работают в поездах при любых скоростях. Масса колодки и расход стального проката на каждую колодку уменьшаются примерно на 1 кг.
4.3.6. С какой целью в местах соединения подвесок триангелей грузовых вагонов с кронштейном введены резиновые втулки?
Боковины тележек грузовых вагонов являются необрессоренными, и на них передаются большие ускорения при движении вагона. Особенно неблагоприятные условия возникают при движении по жесткому пути на железобетонных шпалах вагона, имеющего ползуны, навары на поверхности катания колес или более коварный дефект — неравномерный прокат, который внешне ничем не проявляется. Уровень возникающих при этом ускорений достигает (50+70) g. Чтобы защитить подвески триангелей от разрушения, введены демпфирующие резиновые втулки 2 в месте соединения валиком 3 подвески 4 и кронштейна 1 (рис. 24). Одновременно втулка предотвращает износ валика и подвески. После введения резиновых втулок прекратились случаи излома подвесок и падения на путь триангелей.
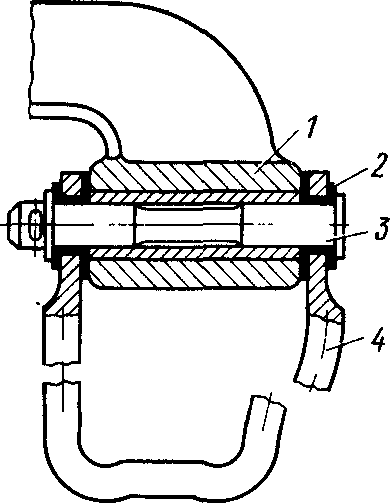
Рис. 24. Резиновые втулки в шарнирах подвесок башмаков грузовых вагонов
4.3.7. В чем особенность работы и преимущества двустороннего нажатия тормозных колодок?
Применение двустороннего торможения обеспечивает меньшие давления в контакте с колесом и уменьшает износ каждой колодки в процессе торможения по сравнению с односторонним нажатием. Особенно существенно это преимущество при чугунных тормозных колодках на крутых затяжных спусках и длительных торможениях, а также при высоких скоростях движения.
На равнинных же профилях пути общий весовой износ тормозных колодок при двустороннем нажатии больше, чем при одностороннем. Учитывая это, а также простоту конструкции, на грузовых вагонах одностороннее нажатие тормозных колодок находит преимущественное применение. Кроме того, при композиционных тормозных колодках одностороннее торможение обеспечивает лучшие условия охлаждения колес.
4.3.8. В чем преимущества дискового тормоза перед колодочным?
При возрастании скоростей движения пассажирских поездов свыше 120 км/ч необходимая эффективность тормозных средств достигается за счет применения композиционных тормозных колодок или скоростного регулирования тормозного нажатия по типу вагонов международного сообщения западноевропейского габарита и электровозов ЧС2, ЧС4, ЧС200. Недостатком композиционных колодок является повышенное термическое воздействие на колеса, особенно при высоких скоростях движения.
Дисковые тормоза такого воздействия на поверхность колеса не оказывают и поэтому находят широкое применение при скоростях более 160 км/ч. Есть и другое преимущество дискового тормоза — возможность упрощения тормозной рычажной передачи и некоторое замедление нарастания проката колесных пар.
Но у дисковых тормозов в свою очередь есть и недостатки. В частности, коэффициент сцепления колес с рельсами в момент торможения бывает на 10—15%, а на сильно загрязненных участках пути и вдвое меньше, чем при колодочных тормозах. Это объясняется тем, что поверхность катания колеса не очищается, поскольку отсутствует фрикционное воздействие на нее. Поэтому дисковые тормоза обычно применяют в сочетании с противогазным устройством. Современные скоростные системы дисковых тормозов имеют по одной чугунной тормозной колодке, действующей с усилием 1000—1300 кгс на поверхность катания колеса (система колодочно-дискового тормоза). Очистка поверхности катания при помощи дополнительных колодок необходима и для надежного шунтирования рельсовых цепей. Недостатком дискового тормоза является также зависимость тормозной силы от диаметра колес, который изменяется при износе и обточках последних.
4.3.9. Как действует противоюзное устройство тормоза КЕ и как проверить его работу перед отправлением поезда?
Принцип действия противоюзного устройства тормоза КЕ основан на использовании силы инерции массы маховика / (рис. 25) противогазного датчика. При обычном разгоне поезда или его торможении соответственно ускорение или замедление не превышает 1,5 м/с2, колесо вагона и связанная с его осью масса маховика 1 противогазного датчика вращаются синхронно. При заклинивании колеса замедление на его поверхности катания более 8— 10 м/с2. Маховик в этом случае повернется по инерции в сторону движения.
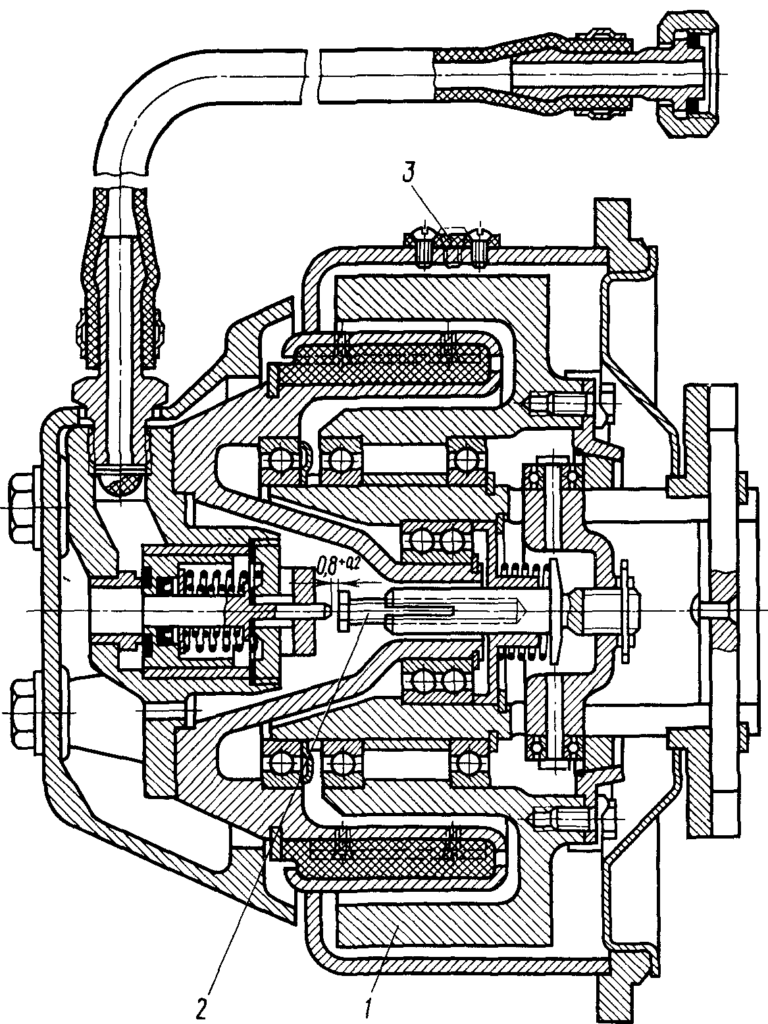
Рис. 25. Осевой датчик противоюзного устройства
Указанный поворот маховика через толкатель 2 воздействует на сбрасывающий клапан и вызывает выпуск воздуха из тормозного цилиндра в течение 0,3—0,5 с.
После возвращения маховика в исходное положение выпуск воздуха из тормозного цилиндра прекращается и происходит его повторное наполнение. Весь процесс протекает очень кратковременно, но за этот период благодаря сбросу давления из тормозного цилиндра прекращается проскальзывание, восстанавливается вращение колеса и вновь повышается давление в тормозном цилиндре. При последующем возможном проскальзывании колеса процесс повторяется. В этом и состоит принцип действия противоюзного датчика.
На корпусе противоюзного датчика имеется резиновая крышка 3. Открыв ее, получаем доступ к маховику. Когда, вагон заторможен, тогда при повороте маховика в любую сторону можно вызвать указанный выше процесс сброса давления из тормозного цилиндра. Об этом свидетельствует звук выходящего воздуха из сбрасывающего клапана и отход колодок от колес. В течение долей секунды после прекращения воздействия маховик займет свое исходное положение, прекратится выход воздуха и колодки вновь прижмутся к колесам. Таким образом, можно проверять действие противоюзного устройства во время стоянки поезда.
4.3.10. Каковы преимущества соединительного рукава тормозной и питательной магистралей с трубкой, имеющей внутренний диаметр 35 мм, по сравнению с трубкой диаметром 32 мм?
Соединительный рукав с трубкой, имеющей внутренний диаметр 35 мм, обладает более высокой надежностью в эксплуатации за счет большей прочности на разрыв в продольном направлении (900—1000 кгс вместо 500—700 кгс), а также в связи с меньшими напряжениями в месте насадки рукава на араматуру. Повышенные напряжения при внутреннем диаметре рукава 32 мм вызывают в некоторых случаях надрыв тканей оплетки на наконечнике арматуры с последующим разрушением рукава. Повышенная жесткость рукава диаметром 35 м обеспечивает его меньшее провисание в расцепленном состоянии (с большим зазором между головкой и путевыми устройствами).